Available as EXTRUDED, including Type 6/6, Type 6 and Type 11; and CAST, including Type 6, Type 6/12 and Type 12; NYLON is, without a doubt, the most common engineering polymer today. NYLON, a crystalline material, possesses many useful characteristics and the wide variety of grades allows for the selection of desirable properties. Generally, tensile properties are high while impact properties are good to excellent. Coefficient of friction is low and abrasion resistance is high making NYLONS suitable for bearings, gears, wear plates and applications where low to moderate loads are operating at low to moderate speeds and at moderate temperatures. All NYLONS absorb moisture to varying degrees. Chemical resistance is good and NYLONS show no stress cracking or crazing when exposed to solvents such as hydrocarbons, ketones or esters. Alkalais and most salt solutions; with the exception of calcium chloride, potassium thiocycnate, lithium bromide and a few others, have no effect. But, strong acids and oxidizing agents will attack the surface and phenols and formic acid will dissolve NYLONS. Electrical insulating properties are good, but these come into consideration when other properties such as mechanical strength, tribiological properties, etc. are also important. Like most polymers, UV radiation deteriorates NYLONS. The addition of carbon black greatly reduces this process.
NYLONS readily accept fillers such as TITANIUM DIOXIDE, used as a nucleating agent to increase crystallinity; MOLYBDENUM DISULPHIDE, used as an internal, dry lubricant to reduce the friction and improve wear resistance; OIL, used as an internal, wet lubricant to reduce the friction and improve wear resistance; GLASS-FIBERS, used to improve tensile properties and dimensional stability; COPPER HALIDES, used to retard thermal oxidative degradation at high temperature exposure, are most common.
The casting method yields higher molecular weight and crystallinity in NYLON resulting in higher physical properties, better chemical resistance and higher heat resistance with better machinability. Massive shapes can be CAST in the simplest of moulds. On the next pages, you can see the difference between EXTRUDED and CAST Type 6. EXTRUSION, on the other hand, is a low cost, volume-oriented process allowing for the creation of small, complex shapes that could not be economically produced by CASTING.
What is meant by the number associated with the "Type" of NYLON? The AMIDE unit is the main group - hence the term Polyamide. AMIDES are separated by METHYLENE groups, which form Polyethylene. The number refers to the METHYLENE groups separating the AMIDE groups. The higher the number; the more METHYLENE units and the more like Polyethylene the NYLON becomes. Tensile properties decrease, impact properties increase, moisture absorption decreases and thermal properties decrease.
READ THIS, IT IS IMPORTANT...
Many properties of NYLONS are very dependent on moisture content and temperature at which the values were determined. As with all the property charts shown, we at Claremont Polymer Shapes have compiled data based on values determined at 20°C/68°F. Since the effect of moisture is negligible on the vast majority of the other polymers considered, we have not included moisture in the normal measuring conditions. But, it is most important to consider moisture with NYLONS. The above data is based, where applicable, on normal environment moisture conditions of 50% relative humidity. Many manufacturers and distributors, though, report values in the "bone dry" or "dry as moulded" condition; both of which mean the same. This practice distorts the comparative value of such data, for normal operating conditions, when evaluating the suitability of NYLONS and other materials. Tensile properties are higher, impact properties are lower and electrical insulation properties are greatly enhanced. Thus, you, as the person trying to make a reasonable selection, are presented with data not useful for comparison. At Claremont Polymer Shapes, we feel strongly that keeping you better informed will benefit us both.
It is important to know that NYLONS, like all polymers, can be coloured. Colour, unless other fillers or reinforcing materials are added, plays no part in physical, electrical, bearing or chemical properties. Colourant may affect the acceptability of a NYLON for direct food exposure. Various manufacturers colour the naturally off-white NYLON either blue or orange or red. If you feel there is a performance difference in an application, either conditions changed when a different colour was used or the grade of NYLON with the different colour contained an additive. Claremont Polymer Shapes can provide you with whichever NYLON colour or brand you request or suggest one based on our experience.
Sine Pump Sleeve
machined from KEVLAR®-FILLED NYLON 6/6
|
HYDLAR® Z is a new NYLON product reinforced with KEVLAR® fibers. HYDLAR® Z has the strength, stiffness, rigidity, toughness, load bearing capability, higher temperature resistance and better dimensional stability normally associated with GLASS-FILLED NYLONS. But, since HYDLAR® Z does not contain GLASS-FIBERS it does not gall mating parts, is much easier on machine tooling and is non-abrasive. Phenomenal wear resistance is the most outstanding property of HYDLAR® Z. In standard thrust washer wear tests, HYDLAR® Z outwears Exturded Type 6 NYLON by 12 to 15 times, outwears Type 6/6 NYLON 8 to 12 times, outwears MoS2-FILLED Type 6/6 NYLON 6 to 9 times and also outwears 30% GLASS-FILLED Type 6/6 NYLON 3 to 4 times! HYDLAR® Z is a product you should be using in your plant and Claremont Polymer Shapes is able to help review your wear problems and show you how to take advantage of products like HYDLAR® Z.
CAST NYLONS are usually manufactured by a simple process which lends itself to short production runs. The process does, however, allow considerable flexibility in that moulds need not be fabricated from much more than metal sheet and large somewhat complicated shapes can be made. In the casting of NYLON, liquid monomer, plus additives is simply poured into a mould which is heated to cause polymerization. A similar process as that used to make a cake! Large bearing sleeves, huge drier gear segments, discharge cams, sprockets, wear plates, coupling box inserts, etc. can be rough cast in NYLON dramatically reducing material costs and fabrication costs. Contact Claremont Polymer Shapes for details on applications that have taken advantage of the CAST NYLON process and we would be pleased to review any of your potential uses.
METHOD FOR BORING POLYMERS
Often machinists damage stock when center drilling EXTRUDED and CAST
NYLONS and other high strength polymers. Heat of friction resulting from drilling dry; or using too large, dull or improperly sharpened drill bits, is trapped in the rod. The heated interior of an improperly bored rod tries to expand. The strong, much cooler exterior of the rod retains the expanding interior causing stress to build up; even if the rod was annealed before drilling began. The hole contracts on the bit; frictional heat build-up increases and the interior of the hole begins to melt. Finally, when this stress exceeds the tensile strength of the rod - it cracks and breaks!
- Use a slow spiral 1/2 inch round bit sharpened for your polymer and NOT USED ON METAL.
- With lubricant on, drill at 1000 rpm with automatic feed of 0.005 inch per revolution.
- Expand hole using a properly sharpened, slow spiral, 1 inch diameter bit at 500 rpm.
- Bore to size using a single point, properly sharpened, boring tool WITH lubricant.
BEARINGS, ROLLERS and GEARS
Much of the information we provided in the section entitled "ACETAL" is applicable to
NYLONS. But there are some important differences and certain properties that should be considered very carefully.
Firstly, NYLONS are tougher; ie. more impact resistant than ACETALS, and as such are preferred for applications in which the parts may be subject to shock. Except for MoS2-FILLED NYLONS, all the other NYLONS have higher notch impact resistance than ACETALS. Hence for parts such as gears possessing a sharp key-way, NYLON, of some type, is probably a better choice. MoS2-FILLED NYLONS in such an application, due to their much higher notch sensitivity would have no better impact strength than ACETALS.
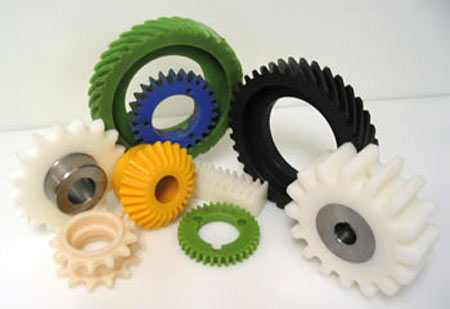
Sprockets and Gears
machined from various FILLED and Non-FILLED NYLONS
|
Secondly, ACETALS do not have the wear resistance toward abrasive particles such as grit, glass, sand, alumina, carton dust, sawdust, cereal-grain dust, etc. that
NYLONS possess. OIL-FILLED CAST
NYLON gears used in agricultural equipment subjected to dirt, MoS
2-FILLED EXTRUDED
NYLON wear plates used glass bottle testing equipment subjected to glass particles and
HYDLAR® Z bearings used in automotive valve stem grinding equipment subjected to grinding wheel dust; perform many times longer than any of the grades of ACETAL.
Thirdly, consider carefully the data when evaluating material for applications at high surface speed. Products such as PTFE-FILLED Poly(AMIDE-IMIDE), 60% Bronze-Filled PTFE, HYDLAR® Z, Graphite-Filled Polyetheretherketone, Graphite-Filled Poly(Ether Sulphone), etc. with outstanding PV limits may out-perform your shaft material. The heat of friction may be so high that the interface temperature where the metal contacts the polymer may exceed the blue brittle point of carbon or alloy steel. Such polymers, because of their nature and with proper design may well survive the heat of friction. But, you will experience a premature failure in your shaft material unless this situation is addressed either by removing heat or changing the shaft material. Similarly, GLASS-FILLED materials should never be used in bearing applications. Simply, glass filaments reinforcing the material will "eat" even shafts hardened to Rc62! There are other reinforced bearing materials such as HYDLAR® Z offering the strength, stability and load handling characteristics that GLASS-FILLED materials offer without the abrasive factor.
Also, some problems presented to NYLONS and ACETALS in shock loading can be overcome. For small parts, Super Tough NYLON ST801 provides very good results as long as high load bearing strength is not required. For small parts requiring higher load bearing strength with shock resistance EXTRUDED NYLON 6 would be a good choice. For higher load bearing, shock resistance and lower coefficient of friction, in larger parts, OIL-FILLED CAST NYLON or Plasticized CAST NYLON may yield good results.
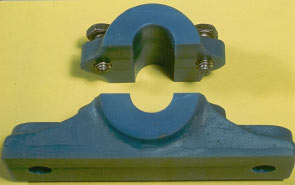
BLUE CAST NYLON 6
pre-CAST and machined Pillow Block Bearing
|
For improved bearing life, an initial application of heavy grease dramatically reduces (about 50%) the coefficient of friction of the system and reduce tendencies toward "slip-stick". In areas where lubrication is not possible or very intermittent, internally lubricated products such as MoS2-FILLED EXTRUDED NYLON, MoS2-FILLED CAST NYLON, OIL-FILLED CAST NYLON, DELRIN 500CL®, DELRIN A/F® and FULTON 404®, can provide significant advantages. All but the OIL-FILLED CAST NYLON use a solid lubricant; only the OIL-FILLED CAST NYLON presents a film of liquid lubricant to the surface bearing on the material. OIL-FILLED CAST NYLON is the only lubricated product in the NYLON/ACETAL group which is approved by USDA for direct food contact.